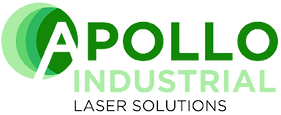
HOW LASER CLEANING WORKS
The laser unit sends high-energy light pulses at the target surface. When this light energy interacts with the contaminants on the surface, the energy is absorbed, and the contaminants will either be vaporised or be removed from the surface due to the pressure of the interaction.
While laser cleaning machines are typically characterized by their wave type, continuous wave or pulse, they are also defined by the two different beam profiles, Gaussian and flat-top, each with their benefits and unique applications.
The Gaussian beam is characterized by a bell-shaped intensity distribution, with a central peak and gradually decreasing intensity towards the edges. Gaussian beams are often used in applications requiring precision, such as laser cutting and engraving, due to the more intense focus of the laser's energy towards the center.
The flat-top beam has a more uniform intensity distribution across its cross-section, resembling a flat plateau rather than a bell curve. It provides a constant intensity over the beam's diameter, making it more delicate than the Gaussian profile.


Our Services
1
PULSED WAVE LASERS
These machines emit laser energy in short, well-defined pulses with a frequency in the range of nanoseconds. This allows for precise removal of contaminants without generating excessive heat, and makes them particularly well-suited for intricate tasks and delicate materials. They can be finely adjusted in terms of pulse duration, repetition rate, and energy output, offering a broad spectrum of applications, such as material processing and accurate surface preparation.
2
CONTINUOUS WAVE
As the name suggests, continuous wave laser machines provide a continuous source of energy to heat and remove the contaminant from the surface of the substrate. These machines are easier to produce and are therefore the lowest cost of the available range of machines.
Improper use may result in notable heat buildup, potentially resulting in thermal harm to delicate materials or affecting the laser's operational efficiency.
3
COMBINATION UNITS
These are a mix of both continuous wave and pulsed lasers to provide the best of both and are typically used in large-scale industrial applications with specialist equipment for automated removal of coatings and contaminants. These are typically in factories, manufacturing plants, and large workshops.
_edited.png)

vs ABRASIVE BLASTING
In comparison to sandblasting, laser cleaning offers significant advantages. Sandblasting incurs high costs (approximately 60% more) in purchasing, collecting, and disposing of the waste media, often necessitating separation from paint debris. Noise and environmental concerns can render many sandblasting applications impractical.
Our lasers resolve the media problem by providing a controlled, non-destructive process suitable for delicate surfaces, thin materials, and composite substrates.
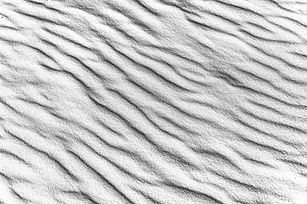
vs WATER/DRY ICE BLASTING
Compared to water and dry ice blasting, our laser systems have faster startup and shutdown times, reducing labor costs and mess. They also offer operator safety features, mitigating the risk of hearing damage and optimizing the use of PPE and laser extraction for environmental control.
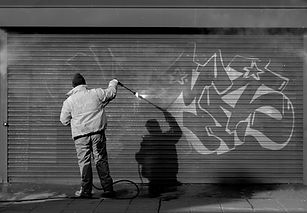
vs CHEMICAL CLEANING
In contrast to chemical cleaning, which struggles with selective application and disposal issues, our lasers can precisely target contaminants without the need for harsh chemicals, ensuring consistent quality and immediate usability.
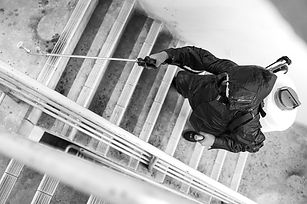
vs THERMAL CLEANING
When compared to thermal heat cleaning, our laser cleaning machines are notably faster and gentler on materials, minimizing the risk of damage, cracking, or distortion. These water-cooled and humidified lasers are versatile, capable of sanitizing and decontaminating a broad range of materials, including dissimilar metals, and effectively removing biofilm or forensic residues.
